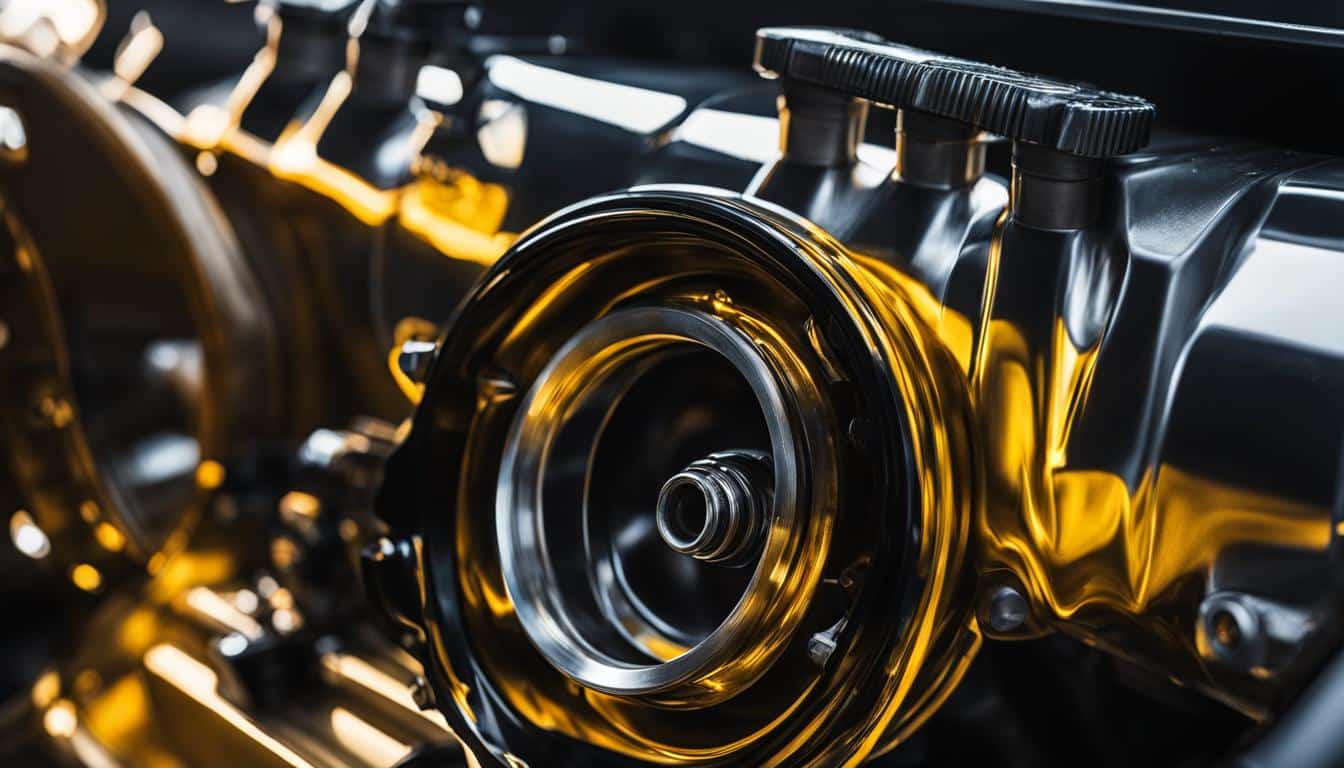
Unveiling Vehicle Lubrication Systems, Oil Myths
Navigating the world of engine oils can be daunting, with one of the most contentious debates revolving around conventional and synthetic oil. This article aims to debunk misconceptions surrounding the safety of switching from conventional to synthetic oil and shed light on the differences between these two types. Additionally, the article explores the roles of additives in both conventional and synthetic oils and how they enhance performance and protection. Knowing the facts about vehicle lubrication systems can help car owners make informed choices about their engine maintenance.
Key Takeaways:
- Understanding the differences between conventional and synthetic oils
- Debunking myths surrounding the safety of switching to synthetic oil
- The role of additives in enhancing engine performance and protection
- Importance of following the vehicle’s owner’s manual specifications
- How to make informed choices about engine maintenance
The Impact of Oil Types on Engine Performance
When it comes to engine oils, the debate between conventional and synthetic oil has long been a topic of contention. However, it is essential to separate fact from fiction to make an informed decision for your vehicle.
Contrary to popular belief, switching from conventional to synthetic oil does not pose a risk to your engine. While early versions of synthetic oils had the potential to dislodge engine sludge and deposits, modern synthetic oils are formulated to be compatible with engines, ensuring optimal performance and protection.
It is crucial to follow the specifications outlined in your vehicle’s owner’s manual when choosing an oil type. This ensures that the oil you choose meets the requirements of your engine and provides the necessary lubrication.
The Differences Between Conventional and Synthetic Oil
Conventional oil is derived from crude oil and undergoes refining processes to remove impurities. It is a tried-and-tested option and can adequately lubricate most engines. On the other hand, synthetic oil is chemically engineered to have uniform molecular structures, resulting in improved performance and protection.
Synthetic oil offers several advantages over conventional oil. It has a higher resistance to breakdown, allowing it to maintain its viscosity and protective properties for a more extended period. Additionally, synthetic oil performs better under extreme temperatures, ensuring optimal lubrication even in harsh conditions. These characteristics make synthetic oil an ideal choice for high-performance engines.
Conventional Oil | Synthetic Oil |
---|---|
Derived from crude oil | Chemically engineered |
Lower resistance to breakdown | Higher resistance to breakdown |
May require more frequent oil changes | Extends oil change intervals |
Performs adequately in most engines | Ideal for high-performance engines |
Understanding the impact of oil types on engine performance is crucial for making informed decisions about your vehicle’s maintenance. By debunking myths and highlighting the differences between conventional and synthetic oil, you can confidently choose the right oil for your engine’s specific needs.
The Role of Additives in Vehicle Lubrication
When it comes to vehicle lubrication, additives play a crucial role in enhancing performance and protection. These additives are carefully formulated compounds that are added to both conventional and synthetic oils to improve their effectiveness in lubricating engines. Understanding the different types of additives and their specific functions can help car owners make informed choices about the oil they use.
One common type of additive found in engine oils is detergents and dispersants. These additives help to clean and remove deposits, sludge, and other contaminants that can accumulate in the engine over time. By keeping the engine clean, detergents and dispersants ensure optimal performance and minimize the risk of engine damage.
Another important additive is viscosity index improvers. These additives help to regulate the oil’s viscosity, ensuring that it remains stable and consistent under different temperature conditions. They prevent the oil from thinning out at high temperatures or thickening too much at low temperatures, thus ensuring proper lubrication throughout the engine.
“Additives in vehicle lubrication systems enhance performance, protect against wear and corrosion, and improve oil flow and lubrication.”
Friction modifiers are additives that reduce friction between moving engine parts. They create a protective layer on the metal surfaces, minimizing wear and tear and improving fuel efficiency. By reducing friction, these additives also contribute to a quieter and smoother engine operation.
Other types of additives include anti-wear agents, antioxidants, rust and corrosion inhibitors, pour point depressants, foam inhibitors, and seal swell additives. Each of these additives serves a specific purpose, contributing to the overall performance and longevity of the engine.
The Role of Additives in Vehicle Lubrication: Table
Additive Type | Function |
---|---|
Detergents and Dispersants | Clean and remove deposits and contaminants |
Viscosity Index Improvers | Maintain stable oil viscosity under different temperatures |
Friction Modifiers | Reduce friction between moving engine parts |
Anti-Wear Agents | Minimize wear and tear on engine surfaces |
Antioxidants | Prevent oil oxidation and degradation |
Rust and Corrosion Inhibitors | Protect against rust and corrosive elements |
Pour Point Depressants | Lower the temperature at which oil thickens |
Foam Inhibitors | Prevent oil foaming |
Seal Swell Additives | Keep engine seals flexible and functional |
The Benefits of Fully Automated Industrial Fluid Coolant Systems
When it comes to maintaining the efficiency and longevity of industrial machines, fully automated coolant systems play a crucial role. By optimizing machine operations, these systems ensure consistent performance and protection, ultimately leading to improved operational efficiency. One of the key advantages of automated coolant systems is their ability to maintain precise coolant concentrations and levels, eliminating the guesswork and inconsistencies that can occur with manual management.
Automated coolant systems are particularly beneficial for addressing labor shortages in manufacturing industries. With these systems in place, workers can focus on more value-adding tasks instead of spending valuable time monitoring coolant levels. This not only enhances productivity but also reduces the risk of human error, ensuring that coolant levels are always within the recommended range. Additionally, by automating coolant management, companies can achieve cost savings by optimizing coolant usage, reducing waste, and minimizing CNC tooling expenses.
The Role of Real-Time Insights
One of the standout features of fully automated coolant systems is the ability to provide real-time performance insights. These systems track coolant levels, temperature, and other critical parameters, allowing for trend identification and data-driven decision making. By analyzing the data generated by the system, manufacturers can gain valuable insights into machine performance, identify potential issues before they escalate, and optimize coolant system maintenance.
Automated coolant systems optimize machine operations, reduce wear and tear, address labor shortages, and achieve cost savings.
Real-time insights also enable proactive maintenance, as any deviations from optimal coolant levels or performance can be quickly identified and addressed. This proactive approach minimizes unplanned downtime, maximizes machine availability, and ensures that cooling systems are functioning at their best. Ultimately, the combination of automated coolant systems and real-time insights empowers manufacturers to make informed decisions, reduce costs, and increase the overall operational efficiency of their facilities.
Benefits of Fully Automated Industrial Fluid Coolant Systems |
---|
Optimized machine operations |
Reduced labor requirements |
Enhanced productivity |
Cost savings on coolant and CNC tooling expenses |
Real-time performance insights |
Proactive maintenance |
The Future of Manufacturing Companies: Investing in Fully Automated Coolant Systems
In today’s rapidly evolving manufacturing landscape, investing in fully automated coolant systems is becoming increasingly essential for companies seeking to optimize their operational efficiency. With the advancements in technology, these automated systems offer a wide range of benefits that traditional manual methods simply cannot match. By streamlining coolant management processes and maximizing machine performance, manufacturing companies can achieve significant cost savings and enhance their overall productivity.
Enhanced Operational Efficiency
One of the key advantages of fully automated coolant systems is their ability to ensure precise coolant levels and concentrations at all times. Manual coolant management can be time-consuming and prone to human error, resulting in inconsistent coolant quality that can negatively impact machine performance and reliability. However, automated systems eliminate these concerns by maintaining optimal coolant conditions consistently, leading to improved operational efficiency.
By investing in fully automated coolant systems, manufacturing companies can achieve greater accuracy in coolant management, reducing the risk of coolant-related issues and costly machine downtime. This enables workers to focus on more value-adding tasks, leading to increased productivity and overall effectiveness.
Cost Savings and Long-Term Sustainability
Automated coolant systems offer significant cost savings for manufacturing companies in several ways. Firstly, by ensuring precise coolant concentrations, these systems prevent over-consumption of coolant, reducing the amount of coolant required and lowering expenses associated with coolant purchase and disposal. Moreover, by maintaining optimal coolant conditions, these systems enhance the longevity of machinery, reducing the frequency of repairs and replacements and contributing to long-term cost savings.
In addition to immediate cost benefits, investing in fully automated coolant systems also promotes long-term sustainability. These systems optimize coolant usage, minimizing environmental impact by reducing waste generation and promoting responsible resource management. By adopting such eco-conscious practices, manufacturing companies can improve their brand image and contribute to a more sustainable future.
Unlocking Competitive Advantage
Manufacturing companies that embrace fully automated coolant systems gain a competitive edge in the market. These systems provide real-time insights into coolant performance and machine health, enabling proactive maintenance and avoiding costly breakdowns. Furthermore, automated systems facilitate data-driven decision making, allowing companies to identify trends, optimize processes, and continuously improve their operations.
Investing in fully automated coolant systems also positions manufacturing companies as industry leaders in innovation and efficiency. By embracing advanced technologies and optimizing their coolant management practices, companies can attract new clients, retain existing customers, and establish themselves as frontrunners in the market.
Benefits of Fully Automated Coolant Systems | |
---|---|
Enhanced operational efficiency through precise coolant management | |
Significant cost savings by reducing coolant consumption and machine repairs | |
Promoting long-term sustainability through responsible resource management | |
Unlocking competitive advantage through proactive maintenance and data-driven decision making |
Conclusion
In conclusion, understanding the intricacies of vehicle lubrication systems is crucial for car owners and manufacturers alike. We have debunked the myths surrounding the safety of switching from conventional to synthetic oil and shed light on their differences. By knowing the facts, individuals can make informed decisions about their engine maintenance.
Additionally, we have explored the vital role of additives in enhancing performance and protection. From detergents and viscosity index improvers to friction modifiers and antioxidants, these additives play a significant part in improving oil flow and lubrication, protecting against wear and corrosion, and maintaining engine efficiency.
Furthermore, investing in fully automated coolant systems can revolutionize industrial applications. These systems optimize machine operations by maintaining precise coolant concentrations and levels, resulting in improved operational efficiency, reduced wear and tear on machinery, and significant cost savings.
Ultimately, by embracing the advancements in vehicle lubrication systems and automated coolant technology, car owners and manufacturing companies can ensure smoother engine performance, longer machinery lifespans, and greater operational efficiency. So, whether it’s engine lubrication or oil changes, staying informed and making the right choices is paramount for a successful and sustainable future.
FAQ
Is it safe to switch from conventional oil to synthetic oil?
Yes, it is safe to switch from conventional oil to synthetic oil. Modern synthetic oils are designed to be compatible with engines and pose no risk to engine performance or longevity.
What are the differences between conventional oil and synthetic oil?
Conventional oil is derived from crude oil and contains impurities, while synthetic oil is chemically engineered and offers better performance and protection. Synthetic oil also has a higher viscosity index, meaning it maintains its performance across a wider range of temperatures.
What role do additives play in vehicle lubrication?
Additives enhance the performance and protection of engine oils. They include detergents and dispersants to clean and prevent sludge formation, viscosity index improvers to improve oil flow, friction modifiers to reduce friction and improve fuel efficiency, and anti-wear agents to protect against engine damage.
Why should manufacturing companies invest in fully automated coolant systems?
Fully automated coolant systems optimize machine operations by maintaining precise coolant concentrations and levels, leading to consistent performance and protection. These systems also reduce wear and tear on CNC machines, address labor shortages, and result in cost savings.
What are the benefits of fully automated coolant systems in industrial applications?
Fully automated coolant systems ensure precise coolant management, eliminate inconsistencies caused by manual maintenance, and free up workers to focus on value-adding tasks. They also result in cost savings on coolant and CNC tooling expenses.