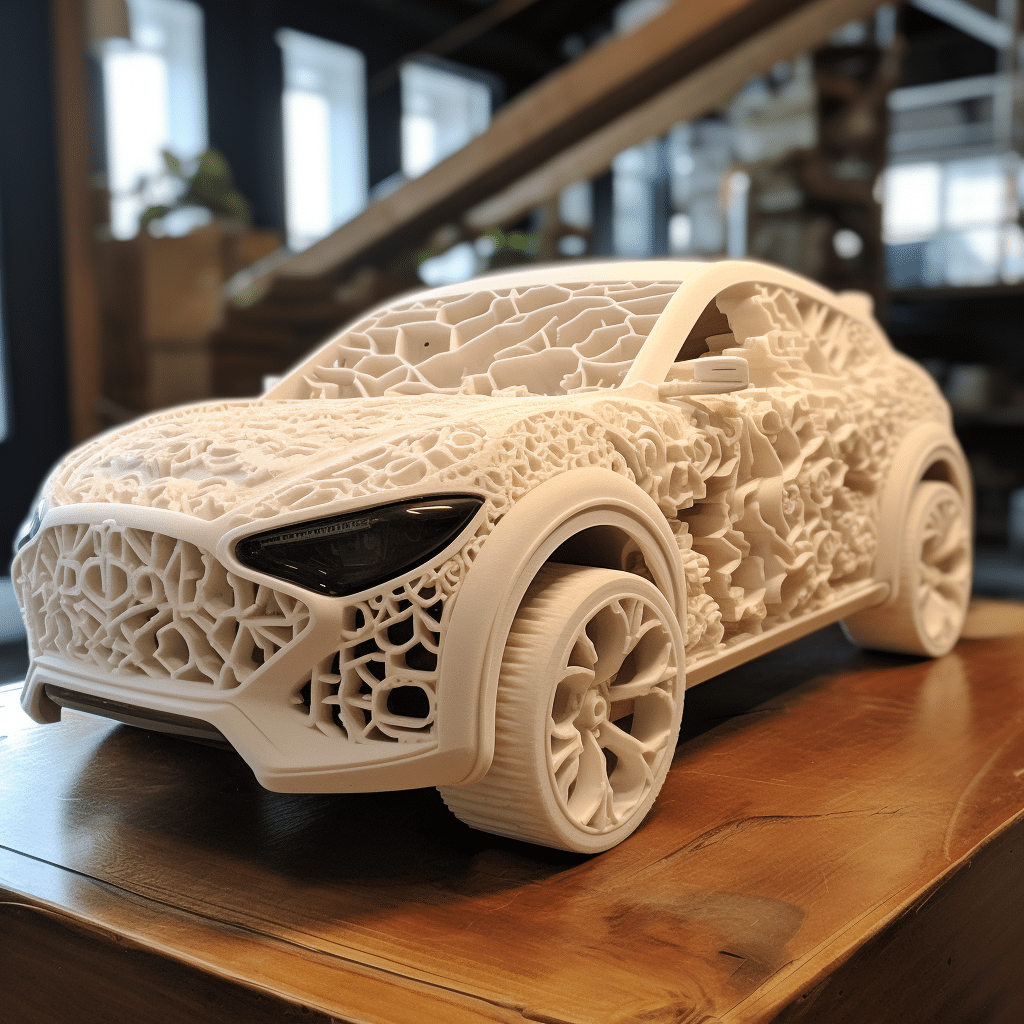
Revolutionizing the Automotive Industry: 3D Printed Car Parts
3D printing has transformed many industries, including the car sector. It offers complex, custom shapes that are useful for producing car parts. Gears, brackets, and larger structural parts can be 3D printed.
A key advantage is the lightweight materials used, such as carbon fiber-reinforced polymers. This leads to greater fuel efficiency and enhanced performance.
Complex designs are now feasible due to 3D printing. Organic shapes and geometries can be created that were impossible or too costly before. This optimizes part functionality and boosts vehicle performance.
Another benefit is the cost-effective production of low-volume or outdated car parts. Automotive companies can print components on demand, reducing lead times and inventory costs.
Interestingly, 3D printing has been used in the automotive industry since the late 1980s. General Motors pioneered this technology with stereo-lithography to make prototype models for testing.
Explanation of 3D Printing Technology
3D printing tech is a revolutionary process that’s become popular. It builds 3D objects by layering materials in a precise way. This tech has enabled car part production, advancing the automotive industry.
The versatility of 3D printing allows intricate and complex car components to be produced easily. Engine parts, dashboard panels, cup holders…all these can be made using this innovative technique. Also, 3D printed car parts can be customized.
An amazing aspect of 3D printing is it can make lightweight but durable parts. Lightweight materials are essential for better fuel efficiency and less emissions in automobiles. With 3D printing, manufacturers can create parts that are strong, reliable and lightweight.
Also, 3D printing for car part production saves time and reduces costs. Traditional manufacturing needs multiple steps and tools, but 3D printing streamlines it into one machine. No need for extensive tooling and assembly processes.
Businesses wanting to implement 3D printing should:
- Invest in advanced 3D printers with a range of materials and large build volumes.
- Collaborate with experienced designers specializing in 3D modeling. Their expertise will help create efficient car parts that integrate into different vehicle models.
- Conduct rigorous quality control tests on 3D printed car parts before integrating into production vehicles. This ensures reliability and durability of parts, and customer satisfaction and safety.
Overview of 3D Printing in the Automotive Industry
3D printing has made massive progress in the auto industry, transforming the way car parts are produced. This article will explain the impact 3D printing has in this sector by discussing its various uses and benefits.
Let’s look at some of the ways 3D printing is used in the automotive industry. The table below gives examples of 3D printed car parts and the advantages they bring:
Car Part | Benefits of 3D Printing |
---|---|
Engine Components | Better performance and custom designs. |
Prototypes | Fast and economical production for testing. |
Exhaust Systems | Lightweight materials for better fuel efficiency. |
Interior Accessories | Able to customize for individual preferences and styles. |
Brake Calipers | Longer-lasting and reduced weight. |
It’s important to note that 3D printing allows for more complicated shapes and intricate designs than traditional manufacturing methods. This versatility enables more innovation in the automotive industry, resulting in more effective and functional vehicles.
In addition to the benefits mentioned, 3D printing also has a more sustainable approach in the auto industry. By using additive manufacturing, manufacturers can cut down on waste compared to traditional subtractive methods. This helps cut costs and lessen environmental impact, making it a great deal.
Specific Car Parts Made Using 3D Printing
3D printing has become popular for manufacturing car parts in recent years. It allows for custom-made components which can improve the car’s performance and aesthetics. Let’s take a look at some car parts made with 3D printing.
Car Part | Material Used | Advantages |
Intake Manifold | Plastic composite | Lower weight and better airflow. |
Gear Shift Knob | Metal alloy or plastic | Customization and ergonomic grip. |
Door Handles | Titanium or aluminum alloy | Lightweight, durable, unique designs. |
Besides these, 3D printing can make engine mounts, brackets, and even entire body panels. Complex geometries and less material waste make 3D printing an attractive option.
It turns out that 3D printing for automotive use began in the 1980s. Ford was among the first companies to use it for prototyping. As technology advanced, more materials and printers were available, leading to wider use of 3D printing for car parts. The automotive industry is looking to this technology to revolutionize production processes.
Advantages and Disadvantages of 3D Printed Car Parts
3D printed car parts can provide unique advantages and disadvantages for the automotive industry. They can offer customization, cost-effectiveness, and reduced waste, but may lack durability and take longer to produce than traditional parts.
Here’s a look at the pros and cons in a tabular format:
Advantages | Disadvantages |
---|---|
Customization | Material Strength |
Cost-Effective | Production Time |
Reduced Waste | Limited Materials |
Innovation Potential | Post-Processing Requirements |
To get the most out of 3D printing, there are a few suggestions that can be made:
- Improve Materials: Develop new materials designed for 3D printing. This could increase strength and durability.
- Optimize Printing: Refine the 3D printing process to reduce production time without compromising quality.
- Collaborate with Traditional Manufacturers: Combining 3D printing with existing methods could enhance efficiency.
Considering these tips can help the automotive industry take advantage of 3D printing while overcoming its limitations. With continuous improvements and increased collaboration, this technology will become more widely adopted.
Future Prospects and Innovations in 3D Printed Car Parts
The possibilities for 3D-printed car parts are limitless! Automotive companies have embraced this technology, leading to amazing progress. Here’s a table of some of the incredible innovations:
Component | Material Used | Advantages |
---|---|---|
Engine Parts | Metal alloys such as titanium or aluminum | Enhanced performance, lighter weight, and lower cost compared to traditionally manufactured parts. |
Exterior Panels | Thermoplastic polymers like ABS or carbon fiber reinforced materials | More durable and resistant to impact while still looking sleek. |
Interior Accessories | Mixed materials including plastics, rubber, and fabric composites | Designs can be customized quickly, with cost-effectiveness for personalized cabin experiences. |
Lighting Systems & Optics | Molded transparent resins or glass-like materials | Advanced lighting with intricate shapes and improved aerodynamics. |
These examples are just a fraction of what is possible. Complex shapes and structures can now be produced that were once impossible. Researchers are also exploring novel ways to use 3D printing in the automotive industry, such as biodegradable materials for interior components.
XYZ Motors faced a supply chain issue with a discontinued engine component. Traditional production methods were out of the question, so they turned to 3D printing. Using laser sintering and high-performance metal powders, XYZ Motors created the complex engine part with even greater strength and durability than the original!
This story shows the amazing potential of 3D printed car parts. As technology advances, we can expect even more progress in manufacturing, customization, and performance optimization. The future of 3D printed car parts is an exciting one, with lots of possibilities for both manufacturers and car enthusiasts.
Conclusion
In the thrilling world of 3D printing, car parts haven’t been left behind. This tech has changed how certain parts are built, providing many advantages. From exterior features like custom grilles and wheel caps, to interior features like dashboard panels and knobs, 3D printing is making its mark in the auto industry.
3D printing offers complex geometries and intricate designs, which were once difficult or costly to make with traditional methods. Now, car lovers can personalize their vehicles with unique, customized parts that reflect their style. From decorative trims to functional accessories, the possibilities are endless.
3D printing creates functional, attractive pieces. Door handles and window switches can be printed on demand, saving time and money. Manufacturing with lightweight, durable materials improves fuel efficiency and performance.
Frequently Asked Questions
1. Do you think it’s possible to build car components using 3D printing?
This innovative technology allows for the creation of complex and customized shapes that may not be feasible with traditional manufacturing methods.
2. Where can you find examples of 3D printed auto parts?
Some commonly 3D printed car parts include interior components like dashboard panels, door handles, and trim pieces. Grilles, spoilers, and mirror housings can be 3D printed. Intake manifolds and brackets are also being 3D printed.
3. In 3D printing, which supplies are used for automobile components?
The choice of materials depends on the desired properties of the car part. Common materials used for 3D printing car parts include various types of plastic, such as ABS and nylon, as well as metals like aluminum and titanium. These materials offer different strengths, durability, and heat resistance.
4.Is the durability of 3D-printed auto parts on par with that of conventionally produced ones?
In some cases, 3D printed car parts can be just as strong as traditionally manufactured ones, if not stronger. The strength of a 3D printed part depends on factors like the chosen material, the printing process, and the design. With proper engineering and material selection, 3D printed car parts can meet or exceed the performance of their conventional counterparts.
5.Are there a lot of 3D-printed auto parts available?
Currently, the availability of 3D printed car parts may vary. While some manufacturers and suppliers offer a range of 3D printed parts, it may still be more common to find traditional, mass-produced car parts. 3D-printed automotive parts will become more accessible as 3D printing technology improves and becomes cheaper.
6. Can I 3D print car parts at home?
Yes, it is possible to 3D print certain car parts at home if you have access to a 3D printer and the necessary design files. However, it is important to consider factors such as the complexity of the part, the required material properties, and legal restrictions. Some car parts may require professional-grade 3D printers or specific certifications to ensure safety and performance.