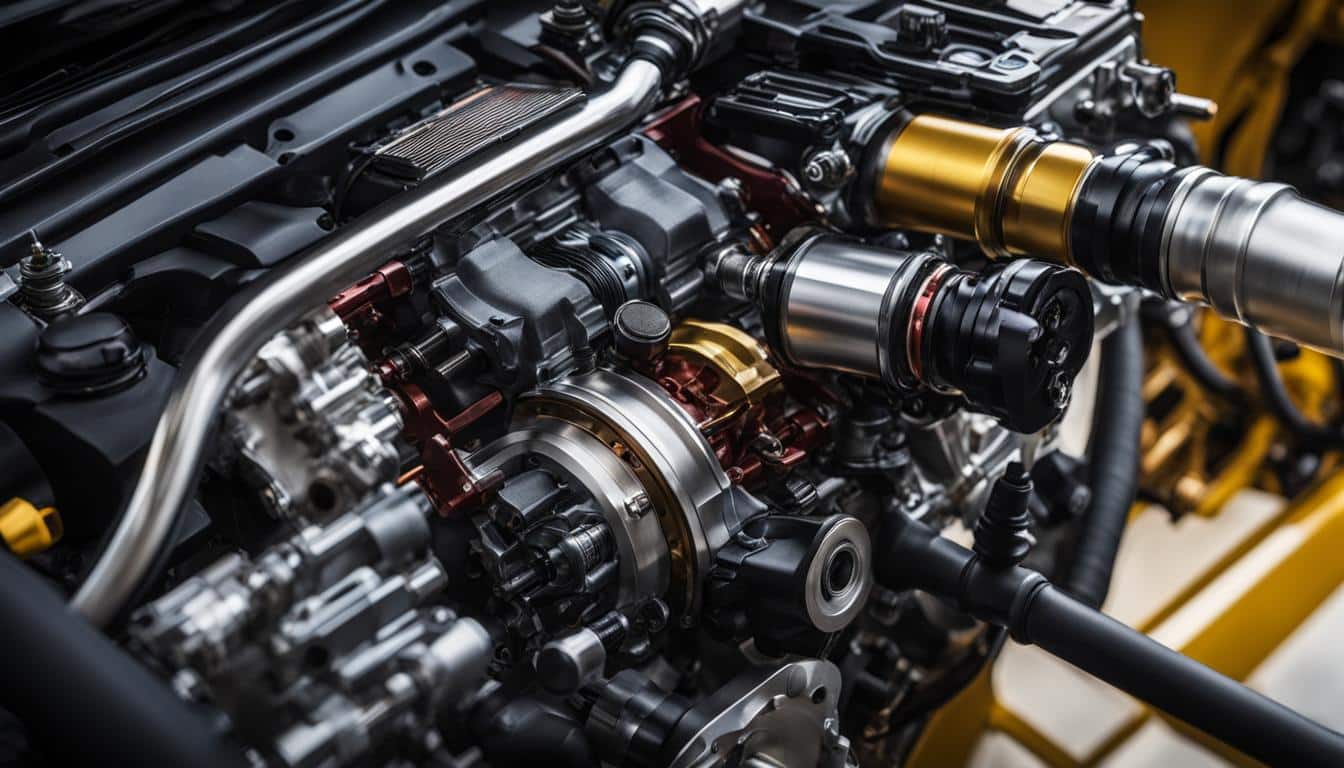
Enhancing Engines: Fuel Injection Systems’ Impact And Evolution
Fuel Injection Systems Evolution: Fuel injection systems are essential components of modern engines, playing a pivotal role in their operation and performance. These systems, controlled by the engine control unit (ECU), ensure precise delivery of fuel to the engine based on various factors such as engine speed, load, coolant temperature, and oxygen level. By calculating the pulse width for fuel injectors, the ECU optimizes fuel efficiency and overall performance.
When it comes to achieving better fuel efficiency, fuel injection systems offer significant advantages compared to traditional carburetors. By precisely controlling the fuel/air mixture, fuel injection systems promote better combustion, resulting in improved efficiency and reduced emissions.
Moreover, fuel injection systems can be enhanced using performance chips that modify fuel maps. However, it’s important to note that these modifications may prioritize performance gains over reliability, mileage, and emissions control.
Key Takeaways:
- Fuel injection systems play a crucial role in modern engines, optimizing fuel delivery for enhanced performance.
- These systems ensure precise control of the fuel/air mixture, leading to improved fuel efficiency and reduced emissions.
- Performance chips can be used to modify fuel maps, but caution is required to balance performance gains with other factors.
How Fuel Injection Systems Work
Fuel injection systems are an essential component of modern engines, ensuring efficient combustion and optimal fuel delivery. These systems can be categorized into two main types: indirect fuel injection and direct injection.
Indirect fuel injection is predominantly used in petrol engines. It involves a fuel pump that sends petrol to the engine bay and injects it into the inlet manifold. This allows for precise control of the fuel/air mixture, resulting in better combustion and improved efficiency compared to older carburetor systems. Carburetors, which were historically used for controlling the fuel/air mixture, have limitations in terms of consistency across all cylinders. In contrast, indirect fuel injection provides more uniform fuel distribution, leading to smoother engine operation and enhanced fuel efficiency.
Direct injection, on the other hand, is primarily used in diesel engines. This method injects fuel directly into the combustion chambers, ensuring thorough mixing with the air for efficient combustion. By injecting fuel directly into the cylinder, direct injection systems achieve better fuel atomization and combustion, resulting in improved power output and lower emissions. This technology has become increasingly popular in recent years due to its ability to optimize engine performance and fuel efficiency.
Type of Fuel Injection | Description |
---|---|
Indirect Fuel Injection | Petrol engines |
Direct Injection | Diesel engines |
How Fuel Injection Systems Work
- Indirect fuel injection involves a fuel pump that sends petrol to the engine bay and injects it into the inlet manifold.
- Direct injection injects fuel directly into the combustion chambers of diesel engines.
Overall, fuel injection systems have revolutionized engine performance, fuel efficiency, and emissions control. Whether through indirect or direct injection, these systems ensure precise fuel delivery, resulting in optimal combustion and improved engine operation.
Components of a Fuel Injection System
A fuel injection system is composed of several key components that work together to deliver fuel to the engine for combustion. Understanding these components is essential for maintaining the proper functioning of the system and optimizing fuel efficiency.
Fuel Injectors
Fuel injectors play a critical role in the fuel injection system. They are responsible for spraying the fuel into the combustion chamber in a fine mist for efficient combustion. Fuel injectors are typically categorized into two types: continuous injection and timed injection. Continuous injection involves a constant flow of fuel into the inlet port, while timed injection delivers fuel in bursts during the induction stroke.
Injection Timing
The injection timing refers to the precise moment when the fuel is injected into the combustion chamber. It is a crucial parameter that directly impacts engine performance and fuel efficiency. The timing is carefully calibrated to ensure optimal fuel-air mixture and combustion. Modern fuel injection systems often utilize advanced electronic control units (ECUs) to accurately control the injection timing based on various engine inputs such as speed, load, and temperature.
Nozzle and Pressure Pipe
The nozzle is a vital component of the fuel injection system. It is responsible for delivering the fuel spray into the combustion chamber. The nozzle design plays a crucial role in achieving the desired spray pattern and atomization of the fuel. Proper maintenance and cleanliness of the nozzle spray holes are essential to prevent disruptions in the fuel flow. Additionally, the pressure pipe carries the fuel from the pump to the fuel valve. It ensures that the necessary pressure is maintained throughout the system for proper injection.
In summary, the components of a fuel injection system, including fuel injectors, injection timing, nozzle, and pressure pipe, work together to ensure efficient fuel delivery and combustion. Understanding these components and their functions is essential for optimizing fuel efficiency and maintaining the performance of modern engines.
Challenges and Advances in Fuel Injection Systems
Fuel injection systems have significantly improved the performance and efficiency of modern engines. However, these systems face challenges such as cavitation, which can impact engine performance and cause various issues like increased noise, vibrations, and surface erosion. To overcome these challenges, advancements in fuel injection technology have been made, resulting in more efficient and reliable systems.
Cavitation in Fuel Injection Systems
Cavitation occurs when a rapid decrease in pressure causes the fuel to vaporize and form bubbles. These bubbles can collapse violently, causing damage to the fuel injection system components. In fuel injection systems, cavitation can be classified into two types: geometric-induced cavitation and vortex cavitation.
Geometric-induced cavitation occurs at the inlet corners of the nozzle holes, where the geometry of the nozzle induces local pressure drops. This type of cavitation can lead to reduced fuel flow and inefficient combustion. On the other hand, vortex cavitation happens in the bulk of the liquid inside the nozzle, resulting in fuel spray disruption and suboptimal combustion.
Advances in Cavitation-Resistant Designs
To address the challenges posed by cavitation, researchers and engineers have developed innovative designs to minimize its effects on fuel injection systems. One approach is altering the curvature of the nozzle hole, which can mitigate geometric-induced cavitation. By modifying the nozzle shape, the pressure drops can be controlled, leading to more uniform fuel flow and improved combustion efficiency.
Moreover, the incorporation of non-cylindrical shapes in the nozzle design has proven beneficial in reducing vortex cavitation. These non-conventional shapes disrupt the formation of vortices, preventing the disruption of the fuel spray. As a result, fuel injection systems equipped with these cavitation-resistant designs exhibit improved performance, reduced emissions, and enhanced durability.
Advancements in Injection System Technology
In addition to cavitation-resistant designs, advancements in injection system technology have contributed to the overall improvement of fuel injection systems. Higher injection pressures, made possible by advanced fuel pumps and injectors, allow for finer fuel atomization, resulting in better combustion and increased fuel efficiency.
Furthermore, electronically controlled injection timing has been an important development in fuel injection systems. By precisely controlling the moment when fuel is injected into the combustion chamber, the system can optimize combustion for different engine operating conditions. This leads to enhanced performance, reduced emissions, and improved fuel economy.
Table: Comparing Cavitation-Resistant Designs
Design | Advantages | Disadvantages |
---|---|---|
Curved Nozzle Holes | Reduces geometric-induced cavitation | Complex manufacturing process |
Non-Cylindrical Nozzle Shapes | Reduces vortex cavitation | Potentially higher manufacturing costs |
In conclusion, fuel injection systems continue to evolve to overcome challenges like cavitation and improve engine performance. Cavitation-resistant designs, such as curved nozzle holes and non-cylindrical shapes, play a crucial role in mitigating cavitation effects. Additionally, advancements in injection system technology, including higher injection pressures and electronically controlled injection timing, further enhance fuel efficiency and emissions control. As research and development in fuel injection systems continue, we can expect even more significant advancements in the future.
Conclusion
Fuel injection systems have revolutionized the performance, efficiency, and emissions control of modern engines. By precisely controlling the fuel delivery, these systems allow for optimal combustion and improved fuel efficiency. Ongoing advancements in fuel injection technology continue to address challenges such as cavitation and further enhance engine performance.
As engines evolve to meet changing requirements and environmental regulations, fuel injection systems will remain vital. Their ability to accurately calculate the pulse width for fuel injectors based on various factors such as engine speed, load, coolant temperature, and oxygen level ensures optimal fuel delivery. This results in improved fuel efficiency, reduced emissions, and better overall engine performance.
Furthermore, fuel injection systems offer the flexibility to modify fuel maps using performance chips, allowing for higher power output. However, it is important to note that modifying fuel maps may prioritize performance over factors such as reliability, mileage, and emissions control. Careful consideration and expert tuning are necessary to strike the right balance.
Fuel injection systems are essential components of modern engines, offering precise control over the fuel delivery process. Advances in technology, including higher injection pressures and electronically controlled injection timing, continue to drive improvements in fuel consumption and emissions control. As the automotive industry continues to evolve, fuel injection systems will play a critical role in meeting the demands of both performance and environmental sustainability.
FAQ
What is the role of fuel injection systems in engine operation?
Fuel injection systems play a crucial role in the operation and performance of modern engines by delivering the right amount of fuel based on factors such as engine speed, load, temperature, and oxygen level.
How do fuel injection systems work in petrol and diesel engines?
In petrol engines, indirect fuel injection involves precise control of the fuel/air mixture by injecting fuel into the inlet manifold. Direct injection, on the other hand, injects fuel directly into the combustion chambers of diesel engines for efficient combustion.
What are the key components of a fuel injection system?
The key components of a fuel injection system include fuel injectors, injection timing, and the pressure pipe. Fuel injectors spray fuel into the combustion chamber, injection timing determines when the fuel is injected, and the pressure pipe maintains the necessary fuel pressure.
What challenges do fuel injection systems face?
Fuel injection systems face challenges such as cavitation, which can impact engine performance and cause erosion. Cavitation can be classified as geometric-induced or vortex cavitation. Advances in design and technology have helped reduce cavitation effects.
How have fuel injection systems revolutionized engine performance?
Fuel injection systems enable precise control of fuel delivery, resulting in optimal combustion, improved fuel efficiency, and reduced emissions. Ongoing advancements in fuel injection technology further enhance engine performance and meet evolving requirements and regulations.