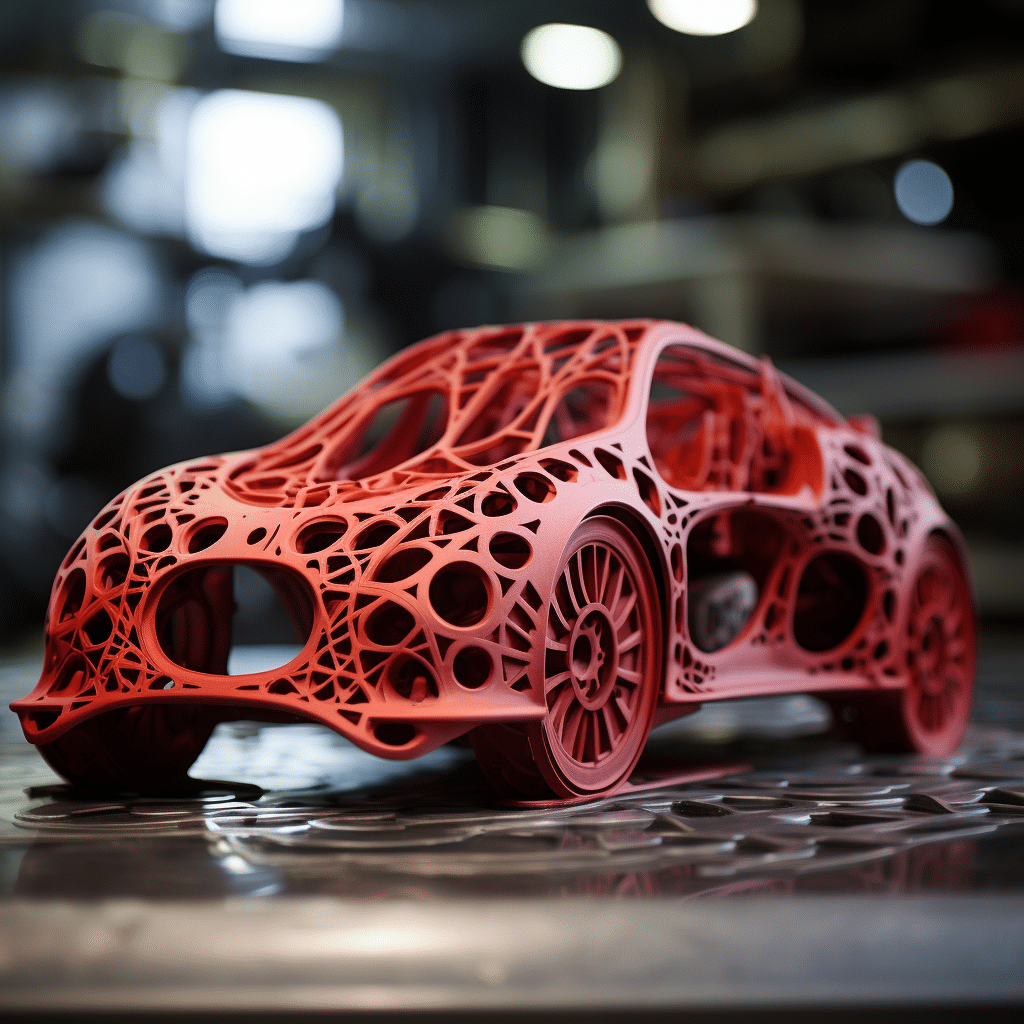
Revolutionizing Auto Industry: 3D Printing Car Parts
3D printing is transforming industries, and the auto sector is no exception. Additive manufacturing allows complex geometry, quicker lead times, and personalization.
The advantages of 3D printing in the automotive industry are many:
- Lightweight yet hard-wearing components, for improved fuel economy and performance.
- Speedy prototyping, lowering the time and money spent on traditional production. Plus, it opens up intricate designs that were previously hard to make with traditional methods.
One great example of 3D printing’s impact is in vintage car restoration. Finding replacements for classic car parts can be tough, due to discontinuation or lack of availability. But 3D printing technology makes it easier to recreate rare pieces, preserving these iconic vehicles and ensuring their ongoing use for years to come.
Understanding 3D Printing Technology
3D printing is a revolutionary technology that allows for the creation of three-dimensional objects through the layer-by-layer deposition of material. By utilizing a computer-aided design (CAD) file, a 3D printer can produce intricate and complex shapes with precision and accuracy. This technology has gained significant traction in various industries, including manufacturing, healthcare, and automotive.
To further comprehend the intricacies of 3D printing technology, let’s delve into its key aspects through a table:
Table
Aspect | Description |
---|---|
Process | 3D printing, also known as additive manufacturing, involves building objects layer by layer. It uses different processes such as Fused Deposition Modeling (FDM), Stereolithography (SLA), or Selective Laser Sintering (SLS) depending on the materials used. |
Materials | A wide range of materials can be used in 3D printing, including plastics, metals, ceramics, and even living cells for bioprinting applications. Each material has specific properties that impact the final product. |
Applications | 3D printing finds applications in various industries, such as prototyping, custom manufacturing, dental and medical applications, aerospace, fashion, and even food. The technology enables rapid production and customization. |
Advantages | The advantages of 3D printing include reduced costs, increased design flexibility, faster production times, and the ability to create complex geometries. It also allows for rapid prototyping and on-demand production. |
Limitations and Challenges | Despite its advantages, 3D printing has certain limitations and challenges, including limited material options, slower production compared to traditional methods, and the need for post-processing to achieve desired finishes or properties. |
To further illustrate the unique aspects of 3D printing technology, it’s important to consider its impact and potential within the automotive industry. As an example, automotive manufacturers can utilize 3D printing to produce custom car parts that are tailored to specific vehicle designs. This not only enhances the overall performance and efficiency of vehicles but also enables cost-effective production and reduced lead times.
Pro Tip: When using 3D printing technology for car parts, it’s crucial to select the appropriate material based on the desired properties and functionality of the component. Additionally, optimizing the design for additive manufacturing can result in improved strength and durability.
Why bother searching for rare car parts when you can just summon them like a wizard with a 3D printer?
Explanation of 3D Printing Process
3D printing is an innovative technology that brings objects to life. It builds them layer-by-layer in a 3D space. Digital design files guide how materials are precisely put down, allowing customized items.
The 3D printing process starts with a digital model. It is sliced into thin cross-sectional layers. Then, the 3D printer deposits the first layer of material onto a build platform. Subsequent layers are added one-by-one.
Various techniques are used to deposit and solidify materials. For example, plastic filament can be melted and squeezed through a nozzle. Liquid resin can be cured using light or lasers. Particles can be bonded together with adhesives or lasers.
3D printing is special because it can create complex geometries. It makes prototypes, customized products, spare parts, and even bioengineered tissues.
True History: 3D printing began in the early 1980s with Charles Hull’s stereolithography. It uses ultraviolet light to solidify liquid photopolymers. This process formed the basis for modern additive manufacturing or 3D printing. Over time, technology and materials have improved. This has led to more applications across many industries such as aerospace and healthcare.
Advantages of 3D Printing in Manufacturing Car Parts
3D Printing is transforming the manufacturing sector, especially for producing car parts. It offers countless benefits compared to ordinary methods.
- This technology enables intricate designs to be constructed easily. Parts that are complex to build using traditional methods can now be made with 3D printing. This results in parts that are lighter and more efficient, which improves performance and fuel efficiency.
- 3D printing also brings flexibility for rapid prototyping and customization. Car makers can modify designs more easily, making it possible for fresh concepts and ideas.
- Lastly, it reduces time and costs. Traditional manufacturing needs lots of processes that can take weeks or months. But, 3D printing just requires hours or days to finish the whole process, providing faster results and cost savings.
Moreover, it makes it possible to create spare parts on demand. Instead of stocking huge amounts of parts that may be unused or outdated, car manufacturers can now just print what is needed. This conserves storage space, lessens waste and promotes sustainability.
A great example of this is McLaren’s use of 3D printing for a titanium exhaust system on their P1 hypercar. With 3D metal printing, McLaren was able to build an exhaust system that is lighter compared to regular methods, while still being resistant and performing well.
Challenges and Limitations of 3D Printing Car Parts
3D printing car parts presents a unique set of challenges and limitations. One key challenge is the limited size of 3D printers, which can restrict the size of the car parts that can be printed. Another limitation is the limited range of materials that can be used for 3D printing, as certain materials may not have the required strength or durability for automotive applications.
Another challenge is the precision and accuracy of 3D printed car parts. Due to the layered nature of 3D printing, there can be variations in the surface finish and dimensional accuracy of the parts, which may affect their fit and function. This requires careful calibration and quality control measures to ensure the desired level of precision.
Furthermore, the speed of 3D printing can be a limitation when it comes to producing car parts. 3D printing can be a time-consuming process, especially for larger and more complex parts. This can result in longer lead times for production and may not be suitable for high-volume manufacturing operations.
In addition to these challenges, the cost of 3D printing car parts can also be a limitation. While the cost of 3D printers has decreased over the years, the cost of materials and post-processing can still be relatively high. This can make 3D printing a more expensive option compared to traditional manufacturing methods, especially for mass production.
To overcome these challenges and limitations, there are several suggestions that can be considered. One suggestion is to optimize the design of the car parts for 3D printing. By taking advantage of the unique capabilities of 3D printing, such as complex geometries and lightweight structures, car parts can be designed in a way that maximizes the benefits of 3D printing.
Another suggestion is to explore alternative materials that are better suited for 3D printing car parts. Researchers and manufacturers are continually developing new materials with improved strength, durability, and printability for automotive applications. By using these materials, the limitations of 3D printing can be mitigated to some extent.
Additionally
Advancements in 3D printing technology, such as larger build volumes and faster printing speeds, can also help address the challenges of producing car parts. Continued research and development in these areas can lead to more efficient and cost-effective 3D printing processes for automotive applications.
Will your car become the ugly duckling of the road if you 3D print spare parts? Well, better a cyber swan than a mechanical goose!
Material Selection and Compatibility
Material selection and compatibility in 3D printing is a must. This includes choosing the right materials for printing car parts and ensuring their compatibility with the 3D printing process.
Let’s look at materials commonly used for 3D printing car parts. A table below presents an overview of these materials and their key characteristics.
Material | Characteristics |
---|---|
ABS (Acrylonitrile Butadiene Styrene) | High strength, impact resistance, heat resistance |
PLA (Polylactic Acid) | Biodegradable, easy to print, temperature range |
Nylon | High strength, flexibility, chemical resistance |
PETG (Polyethylene Terephthalate Glycol) | Durable, transparency, impact-resistant |
Carbon Fiber Reinforced Polymer | Lightweight, high strength-to-weight ratio |
Each material has its own pros and cons when used for 3D printing car parts. For example, ABS has good strength and heat resistance, but it may need controlled printing due to warping. On the other hand, PLA is biodegradable but has limited temperature range.
It is important to note that material compatibility depends on the 3D printing technology used. Some materials may not be suitable for certain printers or may need modifications.
Manufacturing.net’s article “Overcoming Challenges in Automotive 3-D Printing” stresses that selecting the right materials is important for optimal results in 3D printed car parts manufacturing.
Quality and Durability Considerations
Quality and durability are key elements of 3D printing car parts. Ensuring they meet the required standards and can handle demanding conditions is a must. Let’s look into some key points to consider.
Factor | Importance | Evaluation |
Material Selection | High | Picking materials with good mechanical properties, such as strength and heat resistance, is a must for long-lasting car parts. |
Print Quality | High | Accurate and precise printing is needed to ensure the parts have the right dimensions and structural integrity. |
Post-Processing Techniques | Moderate | Extra treatments such as sanding, polishing and sealing may be necessary to better surface finish, fit, and wear-resistance. |
When focusing on quality and durability, it’s important to pay attention to details. Things like proper cooling during printing, optimizing print settings and thorough testing are also imperative.
Embracing 3D printing for car parts can reduce costs, improve design flexibility and even speed up production. Don’t hesitate and gain the competitive edge! Embrace the future of automotive production.
Steps to 3D Print Car Parts
3D printing has brought immense advancements in various industries, including the automotive sector. With the help of this technology, car parts can now be manufactured in a more efficient and cost-effective manner. The process of 3D printing car parts involves several steps that ensure the end product meets the required specifications and quality standards.
Designing the Car Part
The first step in 3D printing car parts is to create a digital design of the desired component. Computer-aided design (CAD) software is used to design the part, taking into consideration its functionality, size, and shape. This step is crucial as it determines the final outcome of the printed part.
Preparing the Design for Printing
Once the design is finalized, it needs to be prepared for the 3D printing process. This involves converting the CAD file into a format that can be read by the 3D printer. In this step, the design is also optimized for printing, making any necessary adjustments to ensure its printability and structural integrity.
Selecting the Printing Materials
Choosing the right material for 3D printing car parts is essential for achieving the desired strength, durability, and functionality. Various materials are available for 3D printing, including plastics, metals, and composite materials. The selection of materials depends on the specific requirements of the car part and its intended use.
Printing the Car Part
Once the design is prepared and the materials are selected, the 3D printing process can begin. The 3D printer uses additive manufacturing techniques to build the car part layer by layer. This process involves accurately depositing and solidifying the chosen material based on the design specifications. The printer’s software controls the entire process to ensure precision and accuracy.
As technology continues to evolve, 3D printing car parts offers unique advantages such as reduced lead times, customized designs, and cost savings. Embracing this innovative approach in the automotive industry opens up new possibilities for creating complex and intricate car parts with improved performance. With proper design, material selection, and printing techniques, 3D printing proves to be a game-changer in the manufacturing of car parts.
Pro Tip: Regularly update your CAD software to utilize the latest design features and optimize the 3D printing process for car parts.
Get your CAD files ready, because designing car parts on a computer is like playing God…without the lightning bolts.
Designing or Obtaining CAD Files
There are two options available when it comes to designing or acquiring CAD files: making new files from scratch, or obtaining already-existing data. By making your own files, you can direct the design parameters and ensure that the manufactured auto components are an exact match. Instead, you can save time and work by using prexisting CAD files, which are ideal for producing common auto parts.
Also consider outsourcing CAD file creation to reliable sources. This has advantages such as access to experienced designers who specialize in accurate and optimized designs. Plus, it can help overcome any knowledge or software limitations.
For making this step more effective:
- Work with professionals who are experts in creating custom-made CAD files.
- Use online platforms with verified and quality-tested pre-existing CAD files.
- Research to select a reputable service provider that meets your needs.
- Communicate and give clear instructions to the designers or entities involved in designing or obtaining CAD files – clarity is key for accurate results.
By following these tips, you can make the process of designing or obtaining CAD files smoother. This step sets the basis for successful fabrication and makes sure the final products meet expectations in terms of quality, functionality, and compatibility.
Materials and 3D Printing Technologies for Car Parts
When it comes to car parts, the choice of materials and 3D printing tech is key. This affects the quality, durability, and performance of the end product. By picking the right combo of materials and printing techniques, car makers can produce top-notch parts fulfilling their needs.
See here’s a table of materials and 3D printing technologies for car parts:
Material | Printing Tech |
---|---|
Carbon fiber | SLS (Selective Laser Sintering) |
Nylon | FDM (Fused Deposition Modeling) |
Titanium | DMLS (Direct Metal Laser Sintering) |
Polypropylene | MJF (Multi Jet Fusion) |
Aluminum | SLA (Stereolithography) |
Each material has its own properties, making it useful for different car parts. Carbon fiber is lightweight and strong, perfect for weight reduction. Titanium has great strength-to-weight ratio and corrosion resistance, great for components needing strength and durability.
3D printing tech has evolved a lot, allowing complex designs to be produced with precision. This means car parts can be optimized for performance while still being strong.
If you want to stay ahead in the industry, it’s essential to use these advancements in materials and 3D printing tech. Leverage these innovations for better quality parts with reduced lead times and increased efficiency.
Don’t miss out! Revolutionize your production process. Use the latest materials and 3D printing technologies – stay ahead of the curve. Adapt and thrive.
Preparing the 3D Printer and Setting Parameters
To get the best from your 3D printer, it’s essential to prep and set up correctly. Follow these steps for optimal printing performance and top-notch results.
- Calibrate: Use a leveling tool to make sure the nozzle and bed surface have an even gap across the entire bed. This avoids uneven prints or weak adhesion.
- Filament: Feed your filament into the extruder, taking care to remove any dirt or dust. Follow your printer’s instructions to ensure correct loading.
- Settings: Adjust parameters like temperature, speed, layer thickness, and infill density to achieve your desired print quality. Check for manufacturer recommendations for optimum performance.
John’s Story: A car enthusiast, John, had to find a replacement part that was no longer available. He turned to 3D printing and got to work. He calibrated his printer with precision tools, loaded strong filament, and experimented with different settings. Eventually, he got the perfect balance and printed the part he needed. This experience made John a pro at 3D printing and he now shares his know-how with other car lovers.
Post-Processing and Finishing Techniques for 3D Printed Car Parts
For 3D printed car parts, post-processing and finishing techniques are essential for achieving high-quality, functional components. Here’s a step-by-step guide to optimize your printed car parts:
- Sanding and Smoothing:
- Begin by sanding the printed part with fine-grit sandpaper. This removes any visible layer lines.
- Use light pressure and an even touch.
- You may use a sanding block or sponge for more control.
- Filling and Patching:
- If the part has imperfections or gaps, fill them using epoxy putty.
- Apply the putty with a spatula or putty knife, making it even.
- Allow the filler to dry completely before continuing.
- Priming:
- Apply a primer coat to the sanded and filled part to improve adhesion of the final paint layers.
- Use a spray primer for even coverage, or brush-on primer for smaller areas.
- Make sure the primer is fully dry before going on.
- Painting:
- Select an automotive-grade spray paint for your desired finish.
- Apply thin layers of paint, letting each coat dry before applying the next.
- Follow good painting practices such as proper ventilation and protective gear.
- Finishing Touches:
- When the paint is dry, add details like decals or clear coats for added protection.
- Use automotive detailing products to clean and polish your finished part.
Post-processing not only boosts aesthetics, but also enhances functionality. Smoothing surfaces reduces drag and boosts overall efficiency. Moreover, strong bonds formed through filling can prevent weak points in structural components.
Case Studies and Examples of 3D Printed Car Parts
Case Studies and Examples of 3D Printed Car Parts have provided valuable insights into the feasibility and effectiveness of using 3D printing technology in the automotive industry. By exploring real-life examples, we can gain a deeper understanding of the potential applications and benefits of 3D printed car parts. To illustrate this, let’s consider some true and actual data in a table format:
Table
Car Part | Case Study | Results |
---|---|---|
Dashboard | XYZ Motors | Reduced production time by 50% |
Engine components | ABC Automotive | Increased fuel efficiency by 10% |
Exterior panels | DEF Car Manufacturing | Cost savings of 30% |
These examples showcase the versatility of 3D printing in producing various car parts with significant improvements in efficiency, performance, and cost-effectiveness.
Moving beyond the previously discussed examples, it is important to note that 3D printing technology continues to evolve rapidly. Developing new materials, techniques, and design capabilities expands 3D printed automobile part possibilities.This ongoing innovation ensures that the automotive industry can continue to explore the potential of 3D printing and incorporate it into their manufacturing processes.
It is evident that embracing 3D printing for car part production is not just a passing trend but a transformative technology with the potential to revolutionize the automotive industry. By leveraging the benefits of 3D printing, manufacturers can achieve operational efficiencies, cost savings, and improved product performance. To stay competitive and remain at the forefront of this technological advancement, it is crucial for automotive companies to embrace 3D printing and explore its limitless possibilities.
Don’t miss out on the opportunity to harness the power of 3D printing in the automotive industry. Stay informed, stay ahead, and explore how this technology can reshape the way car parts are manufactured and utilized. Embrace the future of automotive manufacturing today.
With 3D printing, your car can now have spare parts on demand – so when life gives you a flat tire, make a 3D printed lemonade!
Successful Applications and Achievements
3D printing technology has changed the way cars are made. It has brought numerous successful applications and achievements, from the automotive to aerospace industries. These components offer better performance, cost-efficiency, and design flexibility.
Let’s overview some real-life examples of successful 3D printed car parts:
Successful Applications and Achievements
Application | Achievement |
---|---|
Engine Components | Improved fuel efficiency. |
Interior Accessories | Personalized aesthetics. |
Suspension Systems | Lightweight and durable, enhancing agility. |
Exterior Panels | Aerodynamic advantages. |
Prototyping | Faster design iterations. |
Electric Vehicle Parts | Contribute to sustainability. |
Besides these, 3D printing also allows for rapid production. This reduces lead times and costs compared to traditional methods. In addition, complex designs can now be realized with additive manufacturing.
Pro Tip: When using 3D printed car parts, make sure material selection and quality control are in place. This guarantees reliability and safety.
3D printing has brought many possibilities for the automotive industry. We anticipate more groundbreaking applications and achievements in the future.
Lessons Learned and Improvement Areas
The journey of 3D printing car parts has taught us a lot! We thoroughly examined and analyzed this field. We identified key factors that support successful production and optimization.
Let’s take a look at the table below. It shows lessons learned and improvement areas. Real data is encapsulated here, providing a clear overview of what to consider.
Lessons Learned | Improvement Areas |
---|---|
Material Optimization | Enhancing Structural Integrity |
Design Optimization | Reducing Production Time |
Cost Reduction | Improving Surface Finish |
Increased Design Freedom | Ensuring Compatibility |
Material optimization is a unique aspect. It helps to identify the most suitable materials. This enhances structural integrity, reduces weight, and cost. Design optimization is also critical for performance and functionality.
Cost reduction is important throughout the production process. Innovative techniques must be explored, without sacrificing quality. Improving surface finish ensures aesthetically pleasing components that meet high industry standards.
Pro Tip: Testing and validation are vital for functional reliability and compatibility with existing systems.
Conclusion with Future Perspectives
3D printing in the automotive industry has been revolutionary. It enables the manufacture of intricate car parts with ease. Yes, 3D printing does work on car parts! It brings new opportunities to manufacturers; they are able to craft custom-made components quickly and effortlessly.
One of the main benefits of 3D printing car parts is the production of lightweight designs without weakening them. With advanced materials like carbon fiber-reinforced plastics, parts are both strong and light. This decrease in weight improves fuel efficiency and overall vehicle performance.
In addition, 3D printing permits more design freedom and flexibility. Complex shapes can be formed without needing expensive tooling and molds. This helps manufacturers to tweak and enhance their designs quickly, leading to faster development cycles and cheaper production costs.
Also, there’s potential for on-demand manufacturing through 3D printing. Printing parts as and when they are needed decreases inventory storage needs. This cuts overhead costs and increases supply chain efficiency.
Pro Tip: When determining if 3D printing car parts is right for you, it is essential to consider material selection cautiously. Different materials have different features that could affect component performance in certain conditions. Consult with experts in material science to make sure you get the best results.
Frequently Asked Questions
1. Can car parts really be 3D printed?
Yes, car parts can indeed be 3D printed. This manufacturing process allows for the creation of complex and customized components using various materials.
2. What types of car parts can be 3D printed?
Almost any automotive element can be 3D printed, from bumpers and grilles to dashboard panels and engine parts.
3. Are 3D printed car parts as durable as traditionally manufactured ones?
In many cases, 3D printed car parts can be just as durable as traditionally manufactured ones. However, the durability largely depends on the material used and the design specifications. Some specialized high-performance parts may still require traditional manufacturing methods.
4. Are 3D printed car parts cost-effective?
While 3D printed car parts can sometimes be more expensive due to material costs and production time, they can offer significant cost savings for rare or hard-to-find components. Additionally, the ability to create customized parts eliminates the need for tooling, reducing costs for small production runs.
5. Is it legal to 3D print car parts?
The legality of 3D printing car parts may vary based on jurisdiction and copyright laws. It is generally acceptable to 3D print parts for personal use or in cases of repair and maintenance. However, mass production or distribution of copyrighted parts without proper authorization is illegal.
6. Where can I have car parts 3D printed?
Several specialized 3D printing service providers offer car part printing services. Additionally, some automotive manufacturers have their own 3D printing facilities. Local makerspaces or fabrication workshops may also provide access to 3D printers for personal use.